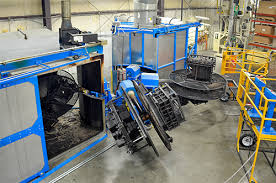
Customization and Flexibility: Meeting Diverse Needs with Rotomolded Products
Plastics rotomolding, or rotational molding, can be a stylish developing approach that involves several specialized factors to be sure the production of higher-high quality plastic material pieces. Comprehending the technical aspects of rotomolding is crucial for refining the method and achieving preferred outcomes. Here’s a closer inspection at some crucial specialized things to consider:
Substance Selection:
Resin Variety: Choosing the right resin is crucial for getting the ideal mechanised properties, chemical opposition, and aesthetics in the closing product or service. Popular resins used in rotomolding include polyethylene, PVC, and nylon material, every giving exclusive features.
Artificial additives: Additives such as UV stabilizers, colorants, and reinforcements can be integrated into the resin to further improve distinct attributes like conditions resistance, coloration consistency, and structural strength.
Mold Style:
Wall surface Density: Maintaining standard wall structure size throughout the part is crucial for guaranteeing structural dependability and avoiding problems including warping and distortion. Suitable mold style, which include sufficient venting and air conditioning channels, helps attain regular walls thickness.
Write Facets: Incorporating draft angles into the fungus design and style facilitates straightforward demolding in the portion and lessens the potential risk of surface area defects or damage during the removing process.
Method Guidelines:
Temperatures Handle: Specific heat control is essential through the cooling and heating levels from the rotomolding approach to attain ideal substance flow, fungus insurance, and component consolidation.
Rotation Speed: Changing the rotation velocity from the fungus factors the submission of the molten resin within the fungus, affecting the wall surface density and general expertise of the done component.
Top quality Confidence:
Inspection Tactics: Applying strenuous examination methods, which include visual inspection, dimensional way of measuring, and screening for mechanical qualities, ensures that the produced parts fulfill high quality specifications and gratification demands.
Procedure Keeping track of: Constant tracking of procedure factors such as temperature, rotation speed, and cycle time assists determine any deviations or inconsistencies early on, enabling timely adjustments and optimization from the approach.
Environmental Concerns:
Material Trying to recycle: Rotomolding is inherently eco-friendly, as it makes minimum waste, and scrap material may be re-cycled and used again from the developing process.
Power Performance: Optimizing approach guidelines and utilizing electricity-efficient air conditioning solutions is effective in reducing electricity consumption and reduce the environment footprint of rotomolding surgical procedures.
In conclusion, Plastics Rotomolding is actually a intricate manufacturing process that needs consideration of varied practical elements to make sure ideal outcomes. By selecting the most appropriate components, developing molds properly, dealing with procedure factors, and utilizing top quality guarantee actions, manufacturers can achieve steady quality, performance, and sustainability in rotomolding operations.